Turning Data into Quality: Inside Premix’s Six Sigma Mindset
A Q&A with Niko Merivirta, Quality Manager & Lean Six Sigma Black Belt at Premix
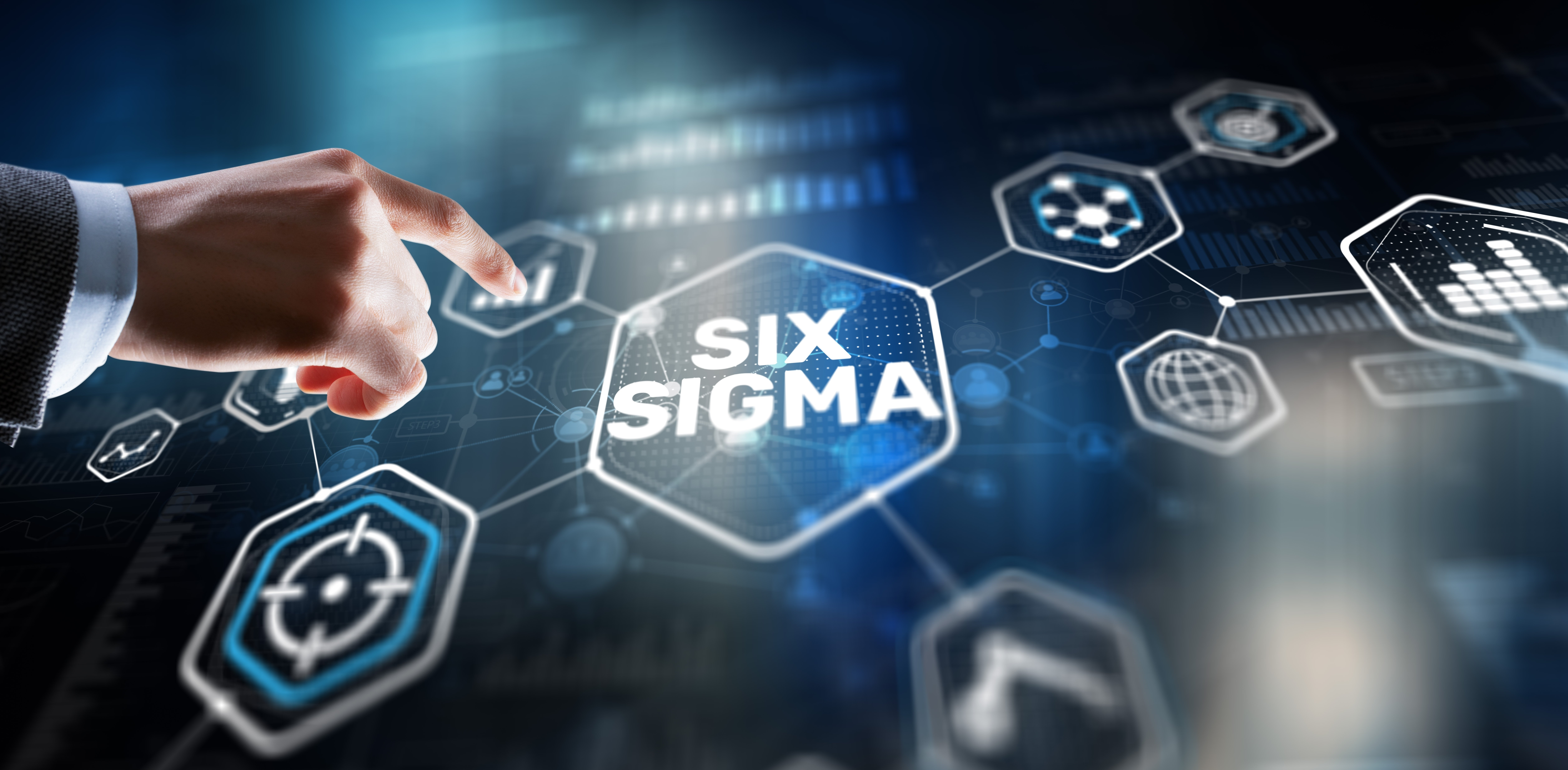
At Premix, quality is more than a checkbox—it’s science. We sat down with Niko Merivirta, our Quality Manager and certified Lean Six Sigma Black Belt, to talk about how data, scientific method, and continuous improvement are helping us deliver industry-leading consistency in conductive plastics.
Q: Niko, let’s start simple. What is Six Sigma, and why does it matter in polymer compounding?
Niko: Six Sigma is a comprehensive set of statistical tools designed to reduce variation, improve process performance and increase profitability. It helps us to identify significant process input and output factors and what is the causality between them. Simplified, it allows engineers to identify how raw materials and compounding parameters in conjunction produce the Critical to Quality properties. In conductive polymer compounding, this means more consistent electrical and rheological properties, reduced off-spec and waste, and faster time-to-validation for our customers.
Q: Can you give us a real example of Six Sigma in action at Premix?
Niko: One example is our project to optimize the compounding process for a key diagnostic-grade material. Using design of experiments tool like the Taguchi L16 design and Statistical Process Control (SPC), we were able to reduce process deviation by ~35% and improve the Cp (process capability) by 57%. That’s a significant leap in quality assurance.
Q: What tools or techniques are part of your Six Sigma toolkit?
Niko: It depends on the problem. We start with DMAIC: Define, Measure, Analyze, Improve, Control. Then we apply the right tools—DOE (Design of Experiments), Ishikawa diagrams, Gage R&R, control charts, and regression modeling (Y = f(X) + ε). For example, we used a Central Composite Design to optimize our U.S. pipette grade to study which process factors and interactions were most critical for the product quality and managed to do a fast scale-up from pilot sampling in Finland to full scale production trials in the U.S.
Q: How does this benefit customers?
Niko: Customers get reliable materials that perform the same way, every time. Whether you’re molding ESD boxes or producing medical devices, Six Sigma gives you more stable and capable process, fewer surprises, and reduced risk. And when we help customers apply these principles in their own processes, they gain cost savings and confidence.
Q: Six Sigma is often seen as an internal toolbox. Do you see it as a customer-facing service too?
Niko: Definitely. While we use it extensively in-house, we also support customers by offering data-driven process optimization as a service. If a customer needs to tune their injection molding parameters or troubleshoot conductivity variations, we can step in with a Six Sigma mindset to help them solve it.
Q: What’s next for Six Sigma at Premix?
Niko: We're expanding the use of real-time online measurement tools and integrating them with SPC systems. This gives us even faster feedback and allows predictive control—catching special cause reasons before they become defects. We're also formalizing how we share Six Sigma knowledge with customers through joint development projects, audits, and training.
Want to learn more? Contact us to optimize your process
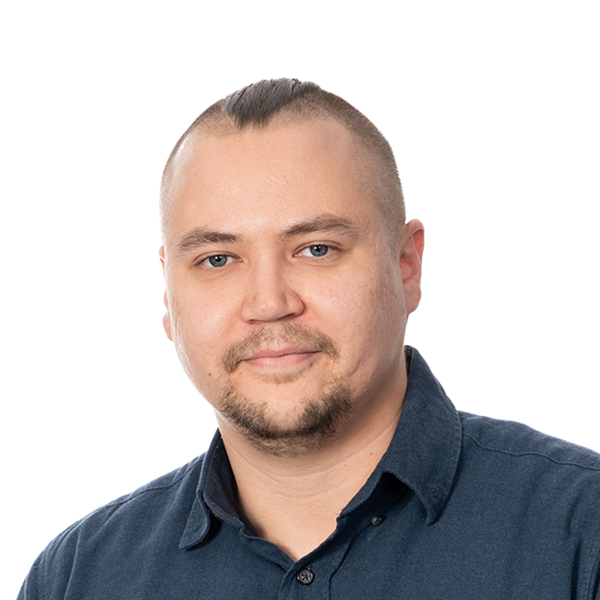
Leave a Reply